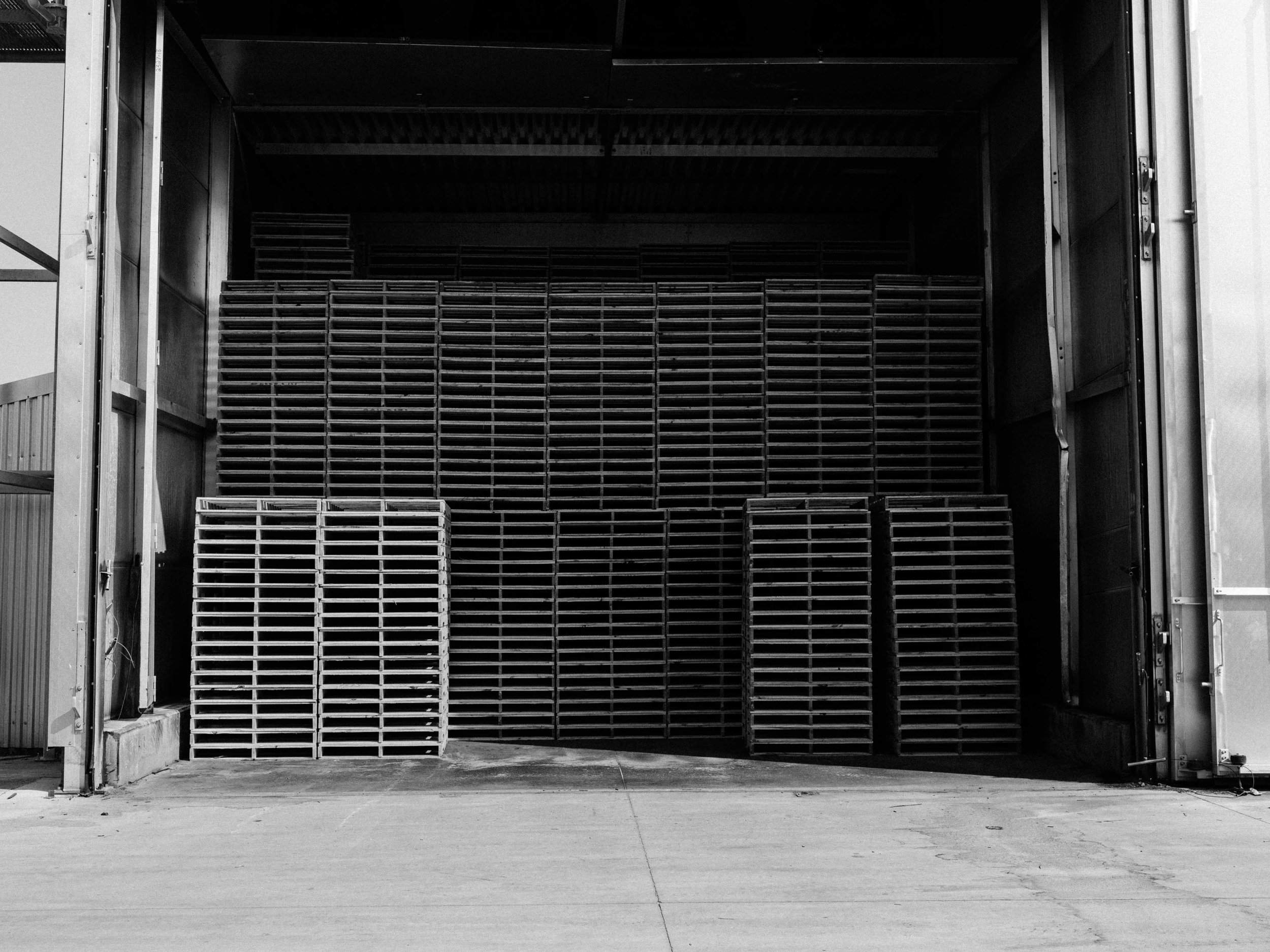
Our Pallet Design
This page assumes the reader has a basic knowledge of stringer style pallets and component terminology.
Variations of the basic 48x40 GMA pallet were for many decades the most widely manufactured pallet in North America. Many other specialty pallets are patterned after it, sharing its basic features: 3 stringers, outside stringers flush with the ends of the deckboards, partial 4-way entry (notched), all three stringers having equal dimensions. An application requiring a stiffer pallet might, for example, specify more and thicker deckboards to achieve the desired strength, or all three stringers might be beefed up for better racking performance under a heavy load. As originally specified, the GMA was actually a very heavy duty, long life pallet. Unfortunately, however, it does not make optimal use of wood fiber, which accounts for 60% to 70% of the cost of a typical pallet. By taking off the blinders and thinking "out of the box" we can dramatically improve pallet performance with some very simple design changes.
One of the most important attributes of a quality pallet is its stiffness. So without going into a highly technical structural analysis, we can improve our pallet design by doing two things: (1) making more optimal use of wood fiber, and (2) increasing pallet stiffness.
A pallet's upper deckboards will transfer the load upon it to the stringers beneath. The load at any given point on the deckboard will, generally speaking, be transferred to the nearest stringer. Thus, for a uniformly loaded, flush, 3 stringer pallet, our stringers will be carrying uneven loads as shown in figure (2). This results in a condition known as "critical stress in the center stringer", meaning that our center stringer is the weakest link in our chain and most likely to fail first. So what are some simple things that we can do to remedy this situation?
One of the easiest ways to remedy this situation is to abandon the notion that our outside stringers should be flush with the end of the deckboards. By moving the outside stringers inward and allowing the deckboard to overhang, we shift some of the load away from the center stringer and onto the outside stringers. This is known as a wing tip configuration. It is possible to precisely position the stringer locations so that the load is evenly balanced across all three stringers, as illustrated in figure (3). In addition to more evenly loading the stringers, we gain two additional key benefits from the wing tip configuration - (1) our nails are now located farther away from the ends of the deckboards, which reduces their tendency to split, and (2) the span between the stringers is reduced, resulting in a much stiffer deck without increasing the thickness of the deckboards. Thus, for no additional wood fiber (translate: no increase in cost), we now have a much higher performance pallet from the exact same components.
Another solution to our unbalanced stringer problem is to make the center stringer thicker than the two outside stringers. However, this solution will give you little or no stiffness benefit and no reduction of deckboard splitting.
FIGURE (1) - A uniformly loaded GMA pallet
Another solution to our unbalanced stringer problem is to make the center stringer thicker than the two outside stringers. However, this solution will give you little or no stiffness benefit and no reduction of deckboard splitting.
For wide pallets supporting heavy loads, you will usually need to increase deckboard thickness to improve pallet stiffness. Don't overlook the possibility, however, of a 4 stringer configuration. We have found that in many applications this is the most economical way to gain the performance advantage required. Figure 4 shows a classic 4 stringer design, although the load is not quite balanced in the stringers (30% on each interior stringer, 20% on each outside stringer). Wing tips can be added to 4 stringer pallets as well in order to more evenly balance these loads. Additional benefits realized from the 4 stringer design include: (1) greater deck stiffness due to reduced span between the stringers, (2) lower potential for lateral collapse due to 1/3 more overall nail joints in the pallet, and (3) a redundancy in the critical center stringer area that may allow for short term pallet survival even if one of the interior stringers should fail. Those customers of ours that we have converted to the four stringer pallet have invariably been very satisfied with the change!
Another design feature of the GMA pallet that is frequently and unnecessarily carried over into specialty pallets is the stringer notch. If you are specifying notched stringers for no other reason than "our pallets have always had notched stringers", then you may be missing the greatest free ride of all. Notches of any kind in the stringers greatly weaken them. It may be well worth your time to review whether or not you really need these notches, or to see if the need for the notch can be eliminated by making some minor equipment or layout changes. These changes may very well pay for themselves many times over by reducing pallet failures and the resulting product damage.
This page has been somewhat of a quick overview of just a few of the key things we commonly look for when assisting our customers in analyzing their pallet requirements. We have both trained specialists and a license to use Virginia Tech's Pallet Design System (PDS). This program can perform very detailed analysis and comparisons of various pallet designs. It will analyze pallets in both stacks and racks, various species of wood, various moisture contents of that wood, various types of nails, conditions of use, etc. It is a predictive tool and field tests of proposed new designs are generally advised.
FIGURE (3) - A wing tip configuration balances the load on the stringers.
FIGURE (2) - Our stringers, however, are NOT so uniformly loaded.
FIGURE (4) - A 4 stringer pallet effectively doubles the critical center stringer.